Toshiba offers an extensive portfolio of motor drivers suitable for the control of brushed DC motors, brushless DC motors and stepping motors. Owing to its unique motor drive technology, Toshiba motor drivers deliver high drive efficiency. Furthermore, these are housed in small packages due to the use of a new analog process. Therefore, they help achieve stable motor control and reduce system size and power consumption.
- TB67H450FNG
- TB67H451FNG
- TC78H653FTG
- TB67S128FTG
- TC78H670FTG
- TC78B009FTG
TB67H450FNG
Brushed DC Motor Driver
Toshiba TB67H450FNG Brushed Motor Driver IC is a Pulse Width Modulation (PWM) chopper Type DC driver. This driver IC is embedded with one channel of H-Bridge and is fabricated with the BiCD process.
This brushed motor driver is rated at output voltage 50V and a maximum current of 3.5A. The TB67H450FNG brushed driver IC features built-in output MOSFETs with low on-resistance and VCC regulator for the internal circuit operation. Features also include error detection functions like Thermal Shutdown (TSD), over current detection (ISD), and Under Voltage Lockout (UVLO).
Buy NowResources:
Features & Benefits
- Monolithic IC using BiCD process
- Capable of PWM constant current drive and direct PWM drive
- Supporting 4 operation modes: forward / reverse / brake / STOP (OFF)
- Built-in H-Bridge MOSFET with Low on-resistance (high side + low side=0.6Ω (typical))
- 4.5V to 44V wide operating voltage
- Low standby current consumption of 1μA (maximum) @ VM=24V, Ta=25°C
- Realization of 3.5 high current drive
- Constant current is adjustable with VREF voltage and sense resistor
- Built-in various error detection functions Thermal Shutdown (TSD), over current detection[1] (ISD), and Under voltage lockout (UVLO)
- Built-in VCC regulator for the internal circuit operation
- Small 8-pin surface mount package HSOP8
Applications
- Industrial equipment including OA equipment and banking terminals; home appliances including robot vacuum cleaners;
- battery powered devices (electronic locks and household small robots), and devices using 5V USB power supplies
Small and Simple DC Brushed Motor Control Driver IC
Notes:
[1] Used to control forward and reverse rotation for DC brushed motors and stepping motors. Transistors and loads have an H-shaped configuration.
[2] The rating in the large mode and the actual motor current are limited by operating conditions such as ambient temperature and power supply voltage
[3] Resistive component when current flows. The lower resistance value achieves a lower loss in motor drives and suppresses heat generation.
TB67H451FNG
PWM Chopper Type DC Brushed Motor Driver
The TB67H451FNG is a PWM chopper type DC brushed motor driver. This product includes one channel of motor output block. Low ON-resistance MOSFETs and a PWM control help the TB67H451FNG exhibit lower heat generation thus efficient motor drive. Furthermore, the TB67H451FNG has two inputs, IN1 and IN2, which allow for selection of the four operation modes; forward (clockwise), reverse (counter-clockwise), short brake, and stop modes.
Fabricated with the BiCD process, the TB67H451FNG is rated at output voltage 50 V, maximum current 3.5A.
Features & Benefits
- Wide operating voltage from 4.5V-44V for USB power, 12V-36 industrial power
- Built-in output MOSFETs with Low on-resistance (High side + low side=0.6Ω(typ.)) for 3.0A applications
- Ultra-low 1uA standby current
- Capable of PWM constant current drive and direct PWM drive
- Supporting 4 operation modes, Forward / Reverse / Brake / STOP (OFF)
- Built-in various error detection functions (Thermal shutdown (TSD), over current detection (ISD), and Under voltage lockout(UVLO))
- Built-in VCC regulator for the internal circuit operation.
- Pin to pin compatible with DRV8870, A4953, A4950
Note: Please be careful about the thermal conditions during use.
Applications:
- Printers, Robotics, Smart locks, Actuators, Surveillance Cameras, Motorized Shades and Blinds, etc.
TC78H653FTG
2-CH Brushed Motor Drivers or 1-Ch Stepper Motor Driver
Toshiba TC78H653FTG dual-H-bridge[1] driver ICs for DC brushed motors and stepping motors that delivers the low voltage (1.8V) and high current (4.0A)[2] essential for low voltage equipment powered by dry-cell or Li-Ion batteries, such as mobile devices, electronic products for the home and USB drives.
Early generations of low voltage motor driver devices have been H-bridge driver ICs constructed with bipolar transistors, which can achieve stable operation at low voltage.
Toshiba’s new dual-H-bridge driver IC uses Toshiba’s specialized DMOS process for low voltage drives to achieve a longer battery life with a stable low voltage operation. Improved motor torque is also realized by reducing IC losses through low on-resistance[3]. The new product is suitable for motor applications driven by relatively low voltage batteries (1.8V to 7.0V).
Buy nowFeatures & Benefits
- Low current consumption prolongs battery life.
- (ICC = 0.6 mA (typ.) in operation mode when VM = 3.0V and Ta = 25°C; ICC = 0 µA (typ.) in standby mode when VM = 3.0V and Ta = 25°C)
- Low on-resistance reduces IC losses generated by voltage drops in the motor driver and increases the voltage applied to the motor, contributing to improved motor torque.
- (Ron = 0.11Ω (typ.) (total of high and low sides in large mode when VM = 5V and Ta=25°C)
- PWM control at 500 kHz is possible by high-speed output switching characteristics (ton = 90 ns, Toff = 90 ns).
Applications
- Motor applications driven by relatively low voltage batteries (1.8V to 7.0V), mobile devices (cameras, electric toothbrushes, printers) using 3.7V lithium-ion batteries, products for the home, such as electronic locks, smart meters, smart water washing, and toys using two 1.5V dry batteries, and devices using 5V USB power supply.
- Products for the home, such as electronic locks, smart meters, smart water washing, and toys using two 1.5V dry batteries, or devices using 5V USB power supply.
TB67S128FTG
Stepper Motor Control Drivers
Toshiba TB67S128FTG Stepper Motor Control Driver is a two-phase bipolar clock-in or SPI serial controlled using a PWM chopper.
This motor driver IC is capable of controlling one bipolar stepping motor. The TB67S128FTG allows full, half, quarter, 1/8, 1/16, 1/32, 1/64, and 1/128 step operations.
Features include built-in anti-stall architecture Active Gain Control (AGC), built-in sense resistor less current control architecture, and high power handling of 50V/5A capabilities.
Buy nowFeatures & Benefits
- PWM controlled constant-current drive
- Low on-resistance (high + low side=0.25Ω (typical)) MOSFET output stage
- Allows full, half, quarter, 1/8, 1/16, 1/32, 1/64, and 1/128 step operation
- High-efficiency motor current control mechanism (Advanced Dynamic Mixed Decay)
- Built-in anti-stall architecture (AGC: Active Gain Control)
- Built-in “sense resistor less current control architecture” (ACDS: Advanced Current Detection System)
- High voltage and current
- Multi error detection functions:
- Thermal Shutdown (TSD)
- Overcurrent (ISD)
- Power-on-Reset (POR)
- Motor load open (OPD)
- Error detection (TSD/ISD/OPD) signal output function
- Built-in VCC regulator for an internal circuit
- Chopping frequency can be customized by external resistance and capacitor
- Thermally efficient with thermal pad package: P-VQFN64-0909-0.50-006
Applications
- 3D printers, surveillance cameras, electric actuators
- Industrial equipment (banking terminals such as ATMs, office equipment, facsimile machines)
- Game machines such as slot machines
TC78H670FTG
Clock-in and Serial controlled Bipolar Stepping Motor Driver
The TC78H670FTG is a two-phase bipolar stepping motor driver using a PWM chopper which incorporate DMOS with low on-resistance in output transistors. The clock-in decoder is built in.
Features:
- Built-in Dual H Bridges, Capable of controlling 1 bipolar stepping motor
- PWM controlled constant-current drive
- Power supply operating voltage: 2.5 V to 16.0 V
- Output current ratings: 2.0 A (max)
- Low on-resistance (High + Low side = 0.48 Ω (typ.)) MOSFET output stage
- Allows full, half, quarter, 1/8, 1/16, 1/32, 1/64, 1/128 step operation
- Built-in Sense resistor less current control architecture (Advanced Current Detection System)
- Multi error detect functions (Thermal shutdown (TSD), Over current (ISD), motor load open (OPD) and Under voltage lockout(UVLO))
- Error detection (TSD/ISD/OPD) flag output function
- Built-in VCC regulator for internal circuit
- Chopping frequency of a motor can be adjusted by external resistor
- Small QFN package with thermal pad (16pin)
Applications:
- Pan Tilt Zoom Cameras
- Portable Printers
- Smart Locks
- Medical Devices
- Small Robotics
Micro-Stepping Motor Driver IC
TC78B009FTG
Sensorless PWM predriver for 3-phase brushless motor
The TC78B009FTG is a 3-phase PWM chopper predriver for sensorless brushless motor. Motor speed can be controlled by selecting among the PWM duty cycle, analog voltage, and I2C. Non-volatile memory (NVM) is implemented and it can set according to the motors and directions for use. It also realizes closed loop speed control function without an external microcomputer. TC78B009FTG is used with six external MOSFETs inverter to drive sensorless brushless motors of which output range is wide.
Features:
- Sensorless PWM drive
- Capable to drive Delta or Wye configured motors
- Operating voltage: 5.5 to 27V (absolute maximum rating: 30V)
- Predriver for high side and low side N-ch MOSFETs drive
- 8 selectable levels of gate drive current
- Built-in closed loop speed control with adjustable speed curve
- Motor speed control by analog voltage, PWM duty cycle, or I2C
- Serial interface (I2C) for various settings
- Standby mode (by STBY pin)
- Current monitor output (PHBF pin)
- CW/CCW control (CWCCW pin)
- Brake input pin (BRAKE pin)
- Rotation speed output (FG pin)
- Abnormality detection output (ALERT pin)
- Thermal shutdown (TSD)
- Under voltage lockout (UVLO)
- Charge pump low voltage detection (CPVSD)
- Output current limit (OCP)
- Over current detection (ISD)
- Lock protection
- Small QFN36 package
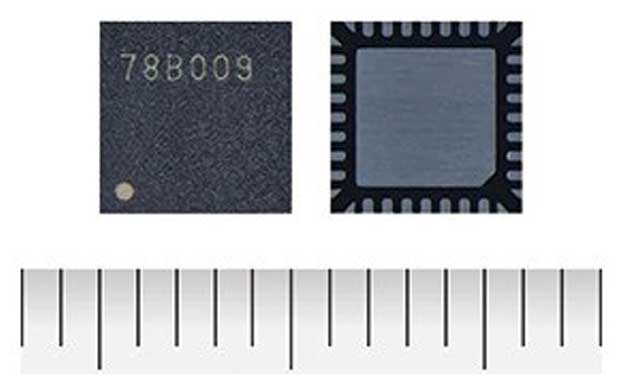
Applications:
- Fan
- Pump
- Portable Vacuum Motors