Connected transportation: Technology solutions to EMI/ESD design challenges for in-vehicle networking IVN
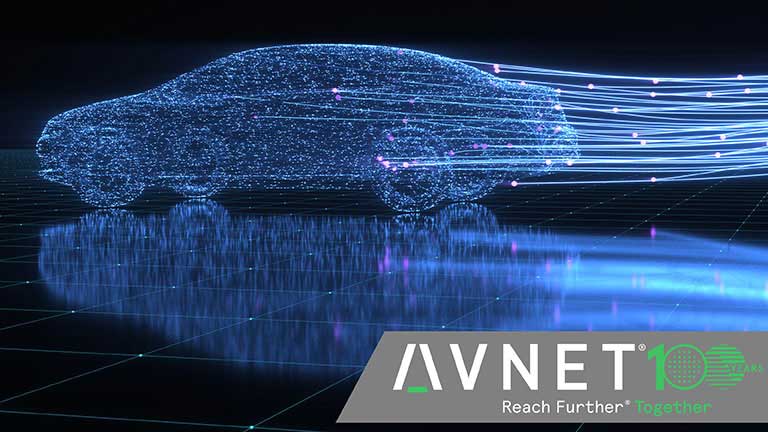
As the number of nodes in IVNs and electronic content under the hood proliferate, electromagnetic interference has greater potential to wreak havoc. Coupled with the ongoing need for reliability, the need to safely manage EMI is an imperative. Suppliers are responding with new solutions.
The growing number of electrical and electronic systems located in the confined space of today’s vehicles poses a challenge in managing both radiated and conducted electromagnetic emissions (EMI), sometimes referred to as crosstalk. If not properly controlled through careful design strategies, EMI events can cause electronic systems to malfunction or fail.
What is EMI/ESD?
Electromagnetic interference (EMI) is also known as radio-frequency interference (RFI). EMI occurs when an RF disturbance in the range of 800MHz to 2GHz is generated by an external source, either natural and manmade, that affects an electrical circuit by electromagnetic induction, electrostatic coupling, or conduction. This disturbance may impair the performance of the circuit or even completely stop it from functioning. In the case of a data path, these effects can range from an increase in error rate to a complete loss of data.
Electrostatic discharge (ESD) is the sudden release of electricity between two electrically charged objects caused by an electrical short, or dielectric breakdown. Static electricity can be defined as a stationary charge that builds up on the surface of a material. The interaction between stationary charges, known as electrostatics, leads to two key problems: electrostatic overstress (EOS) and electrostatic discharge (ESD).
ESD can cause failure and permanent damage to solid state electronic components like integrated circuits. It’s been reported by the ESD Association that ESD causes more than one-third of failures in the semiconductor industry at a cost of nearly $9 billion USD annually.
ESD-induced failures in semiconductors can be seen in the form of leakage, short, burnout, contact damage, gate oxide rupture, and resistor-metal interface damage. CMOS scaling reduces power and increases speed, but smaller size increases susceptibility to damage of the thin gate oxide due to EOS/ESD conditions. The shrinking size of semiconductor chips, thin gate oxides, multiple power supplies, chip complexity, and high-speed circuit operation all contribute significantly to ESD sensitivity. A reduction in gate oxide thickness means less voltage is required to sustain damage.
With ESD, while the amperage might be considered low, it’s not uncommon to have a discharge event that registers in thousands of volts (kV)--strong enough to cause serious damage to circuits, ECUs and other sensitive electronics. The nature of ESD is unpredictable, a charge can be unknowingly carried by a person or object, generated by something as simple as contact with clothing or carpet, and affected by humidity.
Reliable solutions for mitigating EMI/ESD damage
As the number of IVN nodes in the vehicle continues to increase, so does the need for components to pass the required 8kV level of ISO 10605 vehicular system ESD specification. Comprehensive EMI/ESD protection remains a top concern in modern transportation applications.
“Innovative ESD protection structures are available that clamp the transient voltage down to safe levels, implemented either “on-chip” (directly on the IVN transceiver itself) or externally via a standalone ESD protection diode,” said Jeremy Correale, Automotive Product Marketing Engineer, Protection & Signal Division, Power Solutions Group, ON Semiconductor
ON Semiconductor has leading edge solutions that address the unique design challenges of EMI/ESD protection. Transceivers are engineered to be EMI resistant, while ESD events can be controlled by standalone protection circuits.
EMI protection built into leading edge transceivers
ON Semiconductor’s transceivers, for example, pass all transportation OEM requirements for EMI reception and transmission with class-leading performance. Each new generation of transceivers from ON Semiconductor feature continuous design improvements to meet everchanging OEM and government guidelines and regulations.
These include:
- NCV7343: CAN FD Transceivers, High Speed, Low Power
NCV7344: CAN FD Transceivers, High Speed, Low Power
The NCV734x series of CAN transceivers are the interface between a CAN protocol controller and the physical bus. These transceivers provide differential transmit capability to the bus and differential receive capability to the CAN controller.
- NCV7446: Dual CAN FD Transceiver, High Speed, Low Power
NCV7446 is two-channel physical layer device using the CAN protocol. It allows interfacing of two independent CAN physical buses and two independent CAN protocol controllers.
Photo: NCV734x series of CAN transceivers
from ON Semiconductor
Standalone ESD solutions for system-level protection
The continuous drive for miniaturization in the semiconductor industry has rendered device-level ESD solutions alone insufficient to adequately protect electronic devices and systems. The destructive energy associated with an ESD strike is much greater than what can be designed into the miniature silicon of current microcontrollers and chipsets. The best way to address this problem is through system-level ESD protection, accomplished through the addition of cost effective, standalone discrete components that maintain signal integrity and safe operation.
“As more sensors, ECUs, and user interfaces continue to grow in vehicles, so do the chances of ESD events. Choosing the proper ESD protection for your design should not be overlooked. Typically small and inexpensive, these devices can save your company money in the long run and prevent potential safety issues and headaches,” stated Jason Struble, Transportation Supplier Manager, Avnet.
ON Semiconductor, has developed a complete line of standalone ESD protection devices that use advanced diode structures to protect against the damage caused by electrical transients and other current surge pulses.
These include:
Diagram: typical installation of ESD protection diode (NUP2105L)
from ON Semiconductor in an automotive CAN design schematic.
Image courtesy of ON Semiconductor.
Photo: NUP2105L ESD protection circuit from ON Semiconductor
EMI/ESD protection for 10Base-T1S versus CAN
10Base-T1S and CAN XL are two protocols currently competing to bridge the gap between Automotive Ethernet (100/1000Mbs) and 10Mbs in-vehicle networking data rates. When it comes to EMI/ESD protection, there is a difference in architecture between 10/100/1000Mbs Automotive Ethernet (including 10Base-T1S) versus CAN. The integrated circuit (IC) process nodes for 10/100/1000Mbs Automotive Ethernet transceivers are lower than the those for CAN, due to the higher data rate transmission of Ethernet. This makes Ethernet transceivers more susceptible to EMI/ESD damage, but there is a practical solution. The use of ESD circuits with a very low clamping voltage and smaller parasitic capacitance are required for 10/100/1000Mbs Automotive Ethernet transceivers compared to the protection circuits typically used for CAN.
Summary
As the competing formats of 10Base-T1S and CAN XL continue to gain adoption in transportation, and the amount of electronic content in cars continues to increase, solid EMI/ESD protection is required. Adequate EMI/ESD protection requires comprehensive design planning and testing for proper implementation in an IVN design, starting with a thorough review of datasheets and ensuring that the devices under evaluation have been tested by accredited labs such as UL and IBEE. This will safeguard the transmission of data in critical systems, providing for reliable vehicle operation and occupant safety.
Choosing the right technology partners like Avnet and ON Semiconductor for your next transportation application will help you navigate the design complexities along the way to a successful product introduction with a strong competitive edge.
About Avnet
With a century of innovation at our foundation, Avnet can guide you through the challenges of developing and delivering new technology at any — or every — stage of your journey. We have the expertise to support your innovation, turn your challenges into opportunities and build the right solutions for your success. Avnet’s experienced field application engineers are here to help you make the right decision and guide you through the selection process. Make your vision a reality and reach further with Avnet as your trusted global technology partner.



