Robots, reimagined.
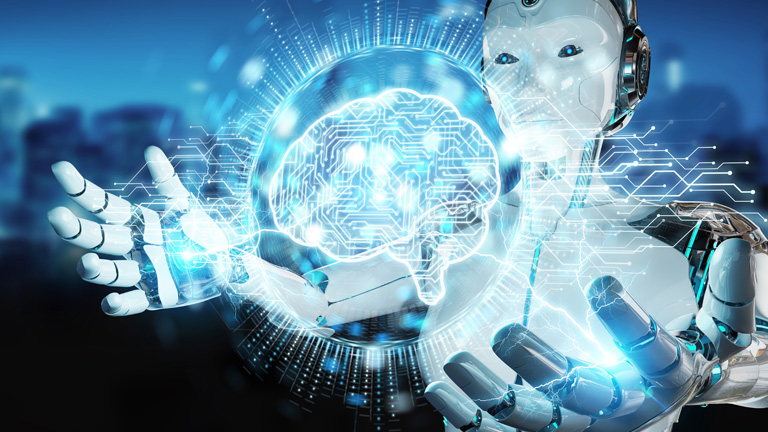
If Industry 4.0 stands at the center of a whirlwind, robots probably stand at “the center of the center.”
Data shows that global sales of robots are projected to skyrocket from US$0.116 billion in 2015 to US$11.4 billion in 2025, representing a market increase of over a hundredfold.
According to Shenzhen Gaogong Industry Research Co., Ltd., in the “world’s factory” of China, robot sales and market scale increased at 91.5% and 71% compound annual growth rates (CAGR) respectively, between 2014 and 2017. By 2020, robot sales are expected to reach 16,500, with a market scale of over US$1.8 billion.
The market data is enough to turn us green with envy. For many, however, the “collaborative robot” or “cobot” is still an alien concept. Effectively, cobots are a new kind of robot that has evolved from traditional industrial robots. However, the roles of cobots differ quite dramatically from those of their predecessors. In some ways they can be regarded as “disruptive” elements in the context of the “Fourth Industrial Revolution.”
Figure 1, Different Types of Cobots (Source: Internet)
Different from the Past
Most people’s impressions of robots can be traced back to the early 1960s, when Unimate arm, a robotic arm, was first installed on an assembly line at General Motors. Since then, robots have replaced human beings in an increasing number of repetitive, dangerous and humanly impossible tasks. They also deliver the “3 highs,” namely high efficiency, high precision and high reliability. Robots have in fact been integral to the modernization of industry. As industrial robots are massive in size and weight, they invariably operate inside a a metal “cage” to prevent causing accidental harm to humans.
In many respects, cobots are the opposites of traditional industrial robots. The word “collaborative” underlines the essential difference between cobots and robots. As their name suggests, the former are no longer “caged” but are able to collaborate closely with humans in the performance of specific tasks. Appearance-wise, cobots look less “aggressive” and more intricate, delicate and gentle than robots.
More flexible and versatile than robots, cobots can take on a variety of roles. They can help humans in performing tasks at which machines excel. In some cases, they can do the same work as humans in order to offset a shortage of manpower. They can even work together with humans to complete a specific task. Collaborative robots, or cobots for short, are truly worthy of their name.
The strongest motivation for developing the new kind of robot, the cobot, was the change in the structure of the global labor force, especially in those industrialized countries where the labor force was dramatically shrinking. The off-shoring of the manufacturing industry due to globalization also exacerbated the risk of domestic manufacturing “hollowing out”, leading to economic and employment crises. When small and medium-sized businesses gradually lost their competitive edge due to the double whammy of a dwindling labor force and increasing costs, it was only a matter of time before the idea of filling the labor gap with low-cost and easily-deployed robots was proposed. And so cobots were born.
It is interesting to note that, after integrating the concept of cobots with Industry 4.0, people have come to realize that the two actually complement each other very well. In many ways, throwing cobots into the mix is like like adding fuel to the fire (in a good way).
Traditional robots | Cobots |
---|---|
Fixed installation, occupy a lot of space |
Concise structure, flexible deployment |
Safety fence is required to allow independent working space |
Able to co-work with people and share working space |
Very difficult to install and deploy |
Quick “plug and play” installation |
High ownership and usage cost |
Low cost and fast return on investment |
Complicated programming instructions and reliance on professional technicians |
Graphic programming with low entry threshold |
Applicable for scale production |
Applicable for small-variety and multi-batch production |
Typical cobot profile
As cobots are a new kind of robot, various industry players would no doubt express varying opinions on what constitutes a cobot. However, most would agree that cobots share the following characteristics.
Human-machine collaboration: Without physical barriers to separate cobots and humans, cobots require safeguards such as advanced sensors that can automatically perceive and adjust to changes in the environment to ensure the safety of both man and machine.
Flexible deployment: Traditional industrial robots complete specific jobs in a largely structured environment, and cannot work without the support of an external operating system. It is generally considered that the cost of the robot itself only accounts for about 30% of the total cost. In other words, even the smallest deployment move of an industrial robot will affect the adjustment of the entire supporting system. On the other hand, cobots can be flexibly deployed and arranged within the available operating space. In most cases, deployment is as simple as “plug and play”. Reliance on professional technicians is thus reduced.
Easy operation: Traditional industrial robots require programming by professional technicians to operate and respond to human commands, as well as additional equipment to make them fully operational. The entry threshold is high. By comparison, cobots feature a friendlier human-machine interface. Graphic programming is often used to complete the configuration of a cobot. Furthermore, the use of VR is on the cards. In the future, via a virtual environment, cobots will be able to learn almost anything through “hands-on teaching.”
Low cost: Not only can a cobot be built at a low price, the cost of building a supporting system is also much lower than for a robot. In reality, there is no need for a professional team of technicians. All in all, the ownership cost is considerably lower. According to estimates from UNIVERSAL ROBOTS, the investment on certain cobots is recouped within an average of 195 days. The ROI data is compelling indeed.
In view of the above, it’s clear that cobots are especially useful for enhancing the efficiency and supporting the manpower of small and medium businesses. Not surprisingly, Taradyne (which acquired UNIVERSAL ROBOTS) revealed in one of its financial statements in 2018 that 50% of their clients who purchased cobots were small and medium businesses. It was only a matter of time before this group of businesses would introduce cobots to a wider range of industries. In addition to typical manufacturing industries like the vehicle and electronic industries, cobots are already being used in warehousing, agriculture and the food and beverage industry.
Figure 2, Abundant Robotics for apple picking. (Source: Internet)
Technical ability empowerment
From the technical perspective, cobots are constantly undergoing improvements that consequently improve their performance as motion controllers, servomotors and reducers. Besides the abilities required to fill these three major roles, cobots may soon acquire another two “abilities” in the future.
The first is the ability to perceive. To truly collaborate with people, cobots need to develop a more advanced visual ability, namely 3D vision. Lidar and other sensors are being incorporated in cobots to enable them to perceive and process more environmental data and thus respond accordingly.
The second is the ability to handle tasks. Basically, traditional industrial robots complete repetitive and predictable tasks. Performing a task without an obvious structure, which is precisely what humans do best, such as selecting an object out of random groups, is not the strong point of a traditional robot. Yet this is just the type of task that cobots will soon master. Adopting artificial intelligence technologies such as machine learning will enhance the ability of cobots to handle non-structural tasks in complex environments.
In short, the era of cobots has dawned. Having a robot like C-3PO from Star Wars to keep you company may not be possible in the foreseeable future. However, having a cobot prepare your daily bento box may soon become a part of the “new normal.”

